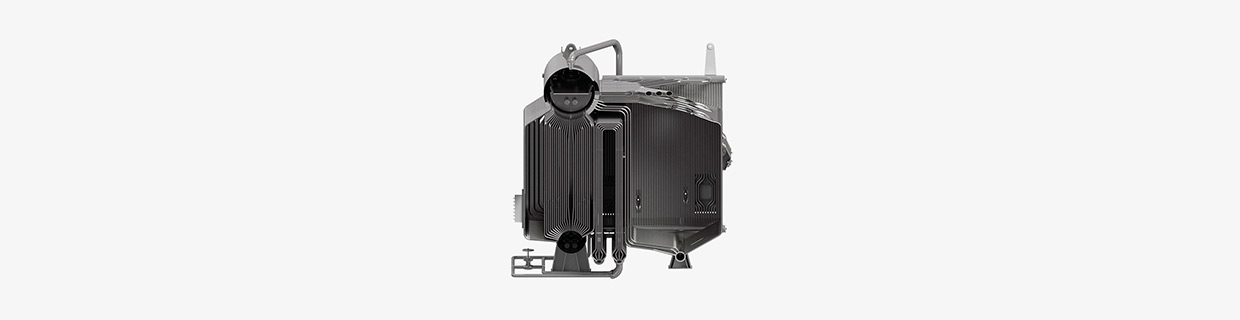
Boilers
Our Services
- Boilers + -
- Waste Heat Recovery(WHR) Solutions
- Heat Exchangers and Condensers
- Heat Recovery Steam Generator (HRSG)
- Module Engineering and Construction
- Process Heaters
- Pipework and Pipe Stress Analysis
- Pressure Vessels and Steel Fabrication
- Skid Manufacture
- Instrumentation Services
- Electrical Switchgear
- Repair and Conversion
- LNG and FLNG Projects
- Project Management
Boiler Surveys, Inspection and Reporting
Our highly qualified and experienced team offer full and comprehensive worldwide inspection and reporting services for industrial and marine boiler plants using state-of-the-art inspection equipment and procedures. In addition to the main boiler component, our capabilities and experience encompass the complete heat transfer and steam system, including the associated piping, valving, combustion and control systems related to the boiler operations.
Harris Pye has extensive experience with boiler systems from all major OEM’s in the industry. Specifically, through an executed service agreement, Harris Pye is a certified partner of Mitsubishi Heavy Industries (MHI) to service their large fleet of boilers installed on assets all over the world.
Apart from normal visual inspection, internal tube inspections are carried out using fiber optic equipment, which is fitted with a video copy processor capable of recording and printing any frame displayed on the screen.
The reports generated from inspections can form the basis of repair specifications used for classifications and underwriting requirements or form a database for future condition monitoring. General marine plants can be surveyed using:
- Optical alignment
- Vibration analysis
- Thermographic analysis
- Analysis of lube oil
Remnant Life Assessment (RLA)
Harris Pye conducts assessments of in-service degradation of crucial and major components that work under harsh temperature, pressure and cyclic stresses, and can lead to creep, fatigue and corrosion issues. The specially designed imaging software enables real-time monitoring of test components as implemented. We are well-adapted to conduct condition assessment and RLA studies given our extensive experience in this field. Non-Destructive Testing such as UT gauging and metallurgical replication can be carried out to assist in determining remnant life of the asset.
NDT Procedures
The inspection process can include various NDT procedures such as:
- Magnetic particle inspection
- Ultrasonic thickness gauging
- Hardness testing
- Tensile testing
- Replica (metallurgical) grain analysis
Boiler Circulation Analysis
We have a global team of steam engineers who can independently assess the internal water circulation of any sub-critical boiler. We use computer-based circulation modelling facility that has been extensively field tested, with both conventional primary element flow measurement equipment and radioactive tracer techniques.
Boiler Troubleshooting and Modelling
By adopting a scientific approach to troubleshooting, we can resolve even the most complex and exclusive issues, including efficiency improvement and redesign whilst still maintaining a remarkably high success rate. The effect of major changes in the heating surface or boiler geometry can be assessed in a matter of minutes, making our equipment an extremely powerful problem-solving tool.
Boiler Design, Tender Preparation, Contract and Site Administration
We are specialist boiler designers, manufacturers and problem solvers. Our team has built and designed boilers for some of the largest boiler companies in the world including B&W, NEI and ICAL. Given our extensive track record, we have developed a reputation in the industry as the go to company for any technical boiler related query.
Many of the problems inherent in a boiler plant are caused by errors of judgement and short cuts taken in original design of the boiler. By correctly specifying the equipment from the outset we can prevent such problems from occurring. Additionally, our independent assessment of the plant can be rectified prior to the boiler coming on-line.
If you are planning on purchasing a new boiler, we are happy to liaise with you at all stages of the boiler construction. We can either design and build your new boiler from scratch or operate independently in the supervision of its design and construction.
This would include the following stages:
- Tender Preparation
- Design appraisal and assessment
- Contract and site supervision
- Commissioning of the plant
- Personnel training
- Ongoing support
Harris Pye Steam Boilers
Steam boilers, which are intended primarily for use on marine installations, can easily be adapted and modified for use in any number of applications where there is a requirement for power and / or process steam. Each boiler package will be custom-designed to meet the requirements of individual customers. We can undertake all aspects of the design in-house. These include – but are not limited to – thermal design and associated activities, skid and module design and layout including stress analysis, as well as naval architecture requirements.
Harris Pye will execute all aspects of design engineering, manufacturing, installation and commissioning, including after-care of the boilers and all associated module plant and equipment. All boilers are designed and manufactured in accordance with ASME and BPVC codes. The boilers and associated equipment are available either fully assembled or in flat pack from Harris Pye manufacturing facilities in the UK, UAE, Saudi Arabia, Singapore or Brazil.
Extended Heating Surfaces – Boiler Components
Harris Pye offers comprehensive design and manufacturing facilities for both plain tube and extended surface exhaust gas economiser assemblies. Extended surface configurations include single and double ‘H’ gilled, spiral wound and serrated type tubes
Helical Solid Fin
Helical solid fin tube is produced on state-of-the-art frequency spiral fin tube welding machines. Tube sizes range from 25mm to 115mm OD and can be found with a range of fin heights from 10- 25mm on varying pitches. This covers virtually all configurations found in marine service today.
Swaged Tubes
Harris Pye can offer manufacturing facilities for swaged tubes for oil fired auxiliary and main boilers. These include ‘Miura’ types tubes and tubes for ‘D’ type main and auxiliary boilers.
‘H’ Fin
Steel ‘H’ fin was introduced in the 1950s due to the requirement for reliability in dirty and potentially corrosive environments, specifically associated with waste heat units fitted to the uptakes of large diesel engines. Harris Pye offers steel ‘H’ Fin design to those in the industry seeking to improve the heat exchange efficiency and extend surface heat transfer.
Pairs of parallel shaped steel fins are resistance-welded to the single pressure tube surface under carefully controlled conditions. The purpose-built welding machine ensure precision indexing along the entire length of the tube and exact parallel attachment. Because of their unique groove structure on the fin surface, ‘H’ type finned tubes have excellent anti-wear and anti-fouling performance.
The ‘H’ design reduces draft loss and allows straight-through flow of gas over the unit. Both factors facilitate a self-cleaning effect, which greatly reduces fouling and the potential for damaging and sometimes catastrophic soot fires. The compact design of these units can realise a 50% saving in space compared to plain tube designs. This is another important consideration in the ever-increasing necessity for space and weight savings.
Our highly skilled and experienced engineers ensure that all stages of programming and works undertaken comply with all the latest class and quality assurance regulations. Our services are guaranteed accordingly. Together with our promise of 24/7 worldwide service, our customers are confident that they can completely rely on Harris Pye in all situations.
HP Economiser Range
The ‘HP’ Economiser range is specifically designed to recover the waste heat in boiler exhaust gases, and to transfer as much energy as possible to the incoming boiler feed water stream by pre-heating the water before it enters the boiler. The design and construction of the HP Economiser lends itself to installation into most boiler exhaust gas outlet ducts. HP high efficiency tube banks are purpose-designed units, constructed from selected finned steel tubing, manufactured on Harris Pye’s own specialised, in-house ‘Spiral’ and ‘H’ type tube finning machines.
Installation of a HP Economiser provides many advantages:
- Reduced energy costs
- For each percentage point efficiency the system gains, an equivalent fuel saving is achieved. i.e. an increase in efficiency of 6% equates to a 6% saving in fuel costs
- Assists with meeting mandatory energy efficiency audit and reporting targets
- Designs are suitable for most fuels
- Less fuel burned results in lower emissions
- Lower CO2
- Lower NOX
- Lower particulates
- Provides the possibility of a carbon offset credit for some operators
HP Economisers are designed and constructed under strict Quality Assurance to meet the highest international standard. They can be comprised of standard carbon steel or high corrosion resistant materials allowing for the highest possible heat recovery with the longest life expectancy. This enables the continued minimisation of your energy costs.